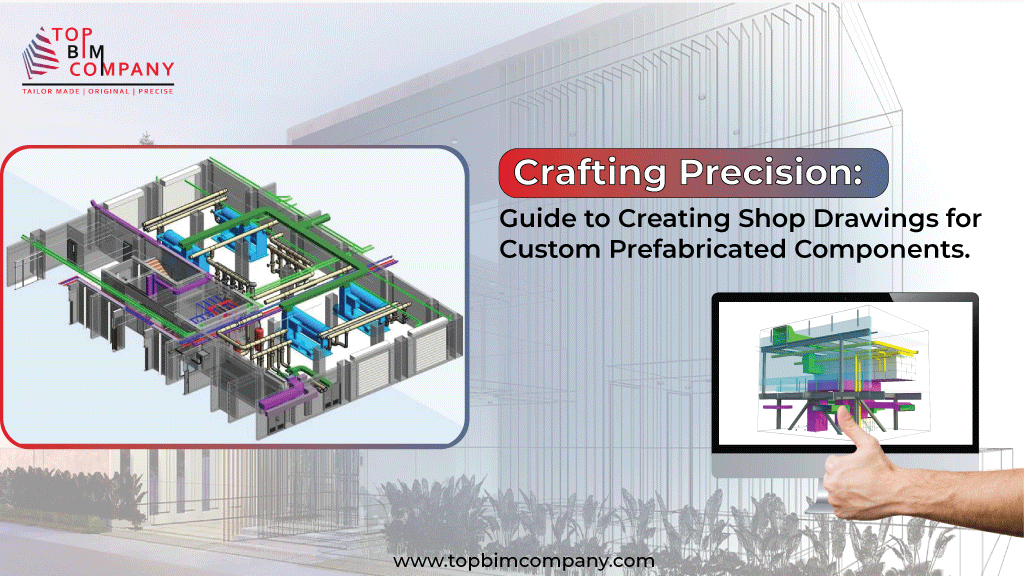
In the dynamic world of construction and manufacturing, the demand for custom prefabricated components is on the rise. These tailor-made elements offer efficiency, quality control, and precise assembly.
Table of Contents
ToggleHowever, to ensure a flawless production process, one crucial element comes into play: shop drawings.
In this comprehensive guide, let’s delve into the art of creating shop drawings for custom prefabricated components, understanding their significance, the step-by-step process, and the tools you need to master this craft.
Understanding the Significance of Shop Drawings
Shop drawings serve as the bridge between design concepts and the actual production of prefabricated components. They are detailed, scaled drawings that provide manufacturers and builders with comprehensive information about how each component should be fabricated and assembled.
These drawings encompass dimensions, materials, connections, and any other crucial details required for production and installation.
Why are Shop Drawings Vital?
- Precision: Shop drawings ensure that each custom component is produced with precision, eliminating errors and discrepancies during the assembly phase.
- Quality Control: They act as a quality control mechanism, allowing manufacturers and builders to verify that the prefabricated components meet design specifications.
- Cost-Efficiency: By offering a clear roadmap for production, shop drawings minimize material wastage and reduce the risk of costly rework.
- Troubleshooting: Shop drawings also serve as a troubleshooting tool, allowing for the identification and resolution of design or fabrication issues before they become on-site challenges.
May be you would like to read –
BIM For Shop Drawings: Accurate, Efficient, And Clash-Free
Ultimate Guide To Create Shop Drawings For Construction
How Digitization Simplifies As-Built Documentation In Construction?
What are Custom Prefabricated Components?
Custom prefabricated components, often referred to as “prefabricated” or “prefab” components, are specialized building elements that are manufactured off-site and then transported to a construction site for installation. These components are designed and built to meet specific project requirements, ensuring they fit perfectly into the construction project.
Examples of custom prefabricated components include:
Image Source: researchgate
- Elevator Systems: Elevators, especially in tall buildings, are often custom-made to fit the exact dimensions and requirements of the structure. They are manufactured off-site, complete with their electrical and mechanical components, and then assembled on location.
- Structural Steel Components: Beams, columns, trusses, and other structural steel elements are fabricated off-site to precise specifications. These components are vital for creating the building’s framework and providing stability and support.
- Modular Building Units: Modular construction involves manufacturing entire sections or rooms of a building off-site, including walls, floors, and ceilings. These modules are then transported and assembled on the construction site to create a complete building.
- Prefabricated Wall Panels: Wall panels, made of various materials like wood, metal, or concrete, are produced off-site and can be quickly assembled to form the building’s exterior and interior walls.
- Pre-Engineered Roof Trusses: Pre-fabricated roof trusses are designed to fit the specific dimensions of the building. They arrive on-site ready for installation, speeding up the construction process.
The benefits of using custom prefabricated components in construction include reduced construction time, improved construction quality and consistency, cost savings, and less waste generated. These components are particularly beneficial in projects with tight schedules and where precision and quality are paramount.
Importance of Shop Drawings:
- Precision: Shop drawings ensure that each custom component is produced with precision, eliminating errors and discrepancies during the assembly phase.
- Quality Control: They act as a quality control mechanism, allowing manufacturers and builders to verify that the prefabricated components meet design specifications.
- Cost-Efficiency: By offering a clear roadmap for production, shop drawings minimize material wastage and reduce the risk of costly rework.
- Troubleshooting: Shop drawings also serve as a troubleshooting tool, allowing for the identification and resolution of design or fabrication issues before they become on-site challenges.
Shop Drawings for Custom Prefabricated Step-by-Step Process
Creating shop drawings for custom prefabricated components is a systematic process that involves several key steps.
Let’s break it down:
- Detailed Review of Design Documents: Begin by thoroughly reviewing the design documents, including architectural and structural plans, to understand the component’s intended use, dimensions, and materials.
- Initial Sketches and Concepts: Create initial sketches and concepts for the custom component based on the design documents. Consider how the component will fit into the overall structure.
- Material Selection: Choose appropriate materials for the component, taking into account factors like durability, cost, and structural requirements.
- Drafting the Shop Drawing: Use CAD (Computer-Aided Design) software to draft the shop drawing. Include detailed information such as dimensions, tolerances, materials, connection points, and any specific assembly instructions.
- Review and Approval: Submit the shop drawing to the design team and the client for review and approval.
- Fabrication and Assembly Instructions: Include clear instructions for the fabrication and assembly of the custom component. This may involve specifying welding techniques, fasteners, and other assembly details.
- Quality Control Measures: Outline quality control measures, including inspections and tests, to ensure that the custom component meets the required standards.
- Final Review and Sign-Off: Conduct a final review of the shop drawing and obtain sign-off from all stakeholders, confirming that it accurately represents the design intent.
- Distribution to Manufacturers: Distribute the approved shop drawing to the manufacturers or fabricators who will produce the custom prefabricated component.
- On-Site Coordination: Coordinate with the construction team to ensure that the custom component is installed correctly on-site, in accordance with the shop drawing.
Software Applications Used to Create Shop Drawings for Prefabricated Components
Creating shop drawings for custom prefabricated components demands the use of specific tools and technologies to enhance accuracy and efficiency:
- CAD Software: Computer-Aided Design software, such as AutoCAD or Revit, is essential for creating precise and detailed drawings.
- 3D Modeling Software: 3D modeling tools help to visualize the component in a three-dimensional space and identify potential issues.
- BIM (Building Information Modeling): BIM platforms provide a collaborative environment for designing, documenting, and sharing information about a project, making it easier to create shop drawings.
- Asset Management Software: Asset management software is used to track and manage the lifecycle of assets, including prefabricated components. Asset management software can be used to generate shop drawings from asset information. Popular asset management software applications include IBM Maximo, SAP Asset Manager, and Infor EAM.
- Prefab Software: Prefab software is specifically designed for the prefabrication industry. Prefab software can be used to create and manage the entire prefabrication process, from design and engineering to fabrication and installation. Prefab software can also be used to generate shop drawings. Popular prefab software applications include StruSoft IMPACT, Trimble Tekla Structures, and Bentley Systems ProStructures.
- Measuring Tools: High-precision measuring tools, including calipers and laser distance meters, are crucial for accurate dimensions.
- Collaboration Software: Tools like BIM 360 or Procore facilitate seamless collaboration amongst project stakeholders.
- Drawing Standards: Familiarity with industry-specific drawing standards and guidelines is essential to ensure compliance with regulations and best practices.
Challenges & Solution of Creating Shop Drawings of Custom Prefabricated Components
While creating shop drawings is a critical aspect of the prefabrication process, it comes with its own set of challenges and best practices:
Challenges:
- Complexity: Custom prefabricated components can be highly complex, requiring meticulous attention to detail.
- Coordination: Coordinating amongst design, fabrication, and installation teams can be challenging.
- Regulatory Compliance: Ensuring that the component complies with local building codes and regulations is vital.
- Accuracy: Mistakes in shop drawings can lead to costly delays and rework.
- Translating On-Site Joinery from the Factory: In some cases, the joinery of pre-fabricated components could be translated badly in the design sheets as a person is assuming on-site work from sitting inside the factory.
Best Practices:
- Early Involvement: Involve the team responsible for creating shop drawings early in the design phase to identify potential issues.
- Communication: Foster open communication among all project stakeholders to address challenges and changes promptly.
- Quality Control: Implement a rigorous quality control process to catch errors before fabrication begins.
- Documentation: Maintain thorough documentation throughout the process, including revisions and approvals.
Creating shop drawings for custom prefabricated components is a meticulous and highly valuable process in the construction industry. It ensures that the end product aligns with design intent, adheres to regulations, and meets quality standards.
By following a systematic approach, utilizing appropriate tools, and adhering to best practices, you can navigate the challenges and reap the benefits of precision, cost-efficiency, and enhanced collaboration in your construction projects.
Our Services
Latest Post
Get A Free Quote
BIM Construction is the Future
Building information modeling (BIM) is the future of building design and construction. Get in touch with our BIM Experts.